3D打印技術(shù)又被稱(chēng)為“增材制造技術(shù)”、“快速成形技術(shù)”和“實(shí)體自由制造技術(shù)”等,至今已有30多年的發(fā)展歷史。3D打印技術(shù)基于離散-堆積原理,以數(shù)字模型為基礎(chǔ),通過(guò)計(jì)算機(jī)程序運(yùn)行使材料逐層熔化和堆積,最終得到立體實(shí)物。相比于傳統(tǒng)的減材制造技術(shù),其最大的優(yōu)勢(shì)在于生產(chǎn)無(wú)需原坯,同時(shí)精度和自由度高、工藝簡(jiǎn)單、節(jié)省時(shí)間及原材料,在航空航天、醫(yī)療、汽車(chē)、國(guó)防、電子等領(lǐng)域得到了廣泛的應(yīng)用,尤其是在一些鏤空多、結(jié)構(gòu)復(fù)雜的結(jié)構(gòu)件上。當(dāng)今,國(guó)內(nèi)外常用的鈦合金
3D打印方法主要有激光選區(qū)燒結(jié)成形技術(shù)(SLS)、激光近凈成形(LENS)、激光選區(qū)熔化成形技術(shù)(SLM)和電子束選區(qū)熔化成形技術(shù)(EBSM),這些技術(shù)都有各自的特點(diǎn),在不同的領(lǐng)域各有優(yōu)勢(shì)。目前可用于3D打印的材料有金屬、高分子、陶瓷、石膏及復(fù)合材料。金屬材料3D打印技術(shù)起步較晚,但發(fā)展迅速,有研究者認(rèn)為金屬材料3D打印技術(shù)可能在快速成形制造領(lǐng)域逐漸占據(jù)主導(dǎo)地位。
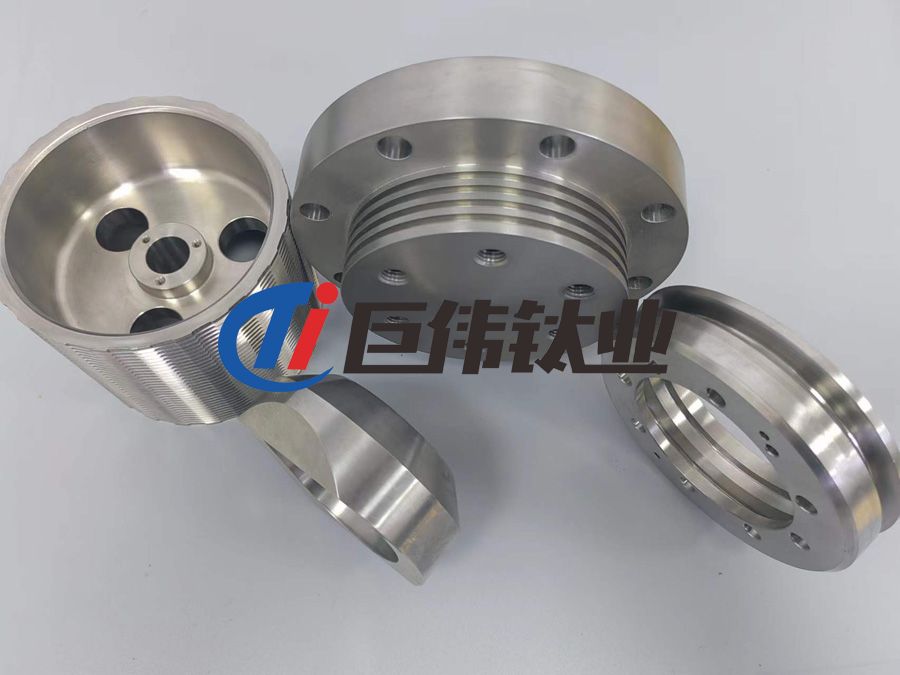
金屬3D打印材料主要集中在鈦合金、鋁合金、鐵基合金領(lǐng)域,其中鈦合金的發(fā)展最快。鈦合金具有密度小、比強(qiáng)度高、耐高溫、耐腐蝕、生物相容性好等特性,在航空航天、船舶與海洋工程、醫(yī)療、石油化工等領(lǐng)域應(yīng)用廣泛。從工業(yè)價(jià)值、資源壽命和發(fā)展前景看,鈦合金僅次于鐵和鋁,被稱(chēng)為“正在崛起的第三金屬”[1~4],但其材料昂貴、加工難度大,采用普通鍛造、機(jī)加方法獲得零件,材料利用率低,制造成本居高不下,限制了其進(jìn)一步推廣應(yīng)用[5]。鈦合金鑄件工藝靈活性好,可以直接近凈成形各種形狀的構(gòu)件,減少機(jī)加工量,提高金屬利用率,并縮短生產(chǎn)周期,有效降低鈦合金零件制造成本。近年來(lái),隨著鑄造技術(shù)提高以及熱等靜壓(HIP)等工藝的應(yīng)用,鈦合金鑄件品質(zhì)及性能已經(jīng)接近鍛件的水平,且裂紋擴(kuò)展和抗蠕變性能優(yōu)于相應(yīng)的鍛件[6,7],加速了鈦合金鑄件在航空發(fā)動(dòng)機(jī)、導(dǎo)彈、衛(wèi)星及人體植入物等領(lǐng)域的應(yīng)用[8~10]。同時(shí),隨著3D打印技術(shù)的發(fā)展及推廣,其快速制造、復(fù)雜結(jié)構(gòu)零件成形方面的顯著優(yōu)勢(shì),為鈦合金鑄件生產(chǎn)工藝革新,提供了新的發(fā)展機(jī)遇[11,12]。
國(guó)際上3D打印技術(shù)在鈦合金加工成形上的應(yīng)用主要有:①直接3D打印鈦合金構(gòu)件,采用SLS并選擇合適的鈦合金粉末,根據(jù)設(shè)計(jì)好的三維零件圖形通過(guò)激光源提供的能量使得鈦合金粉末燒結(jié)成形,逐層打印出鈦合金構(gòu)件;②3D打印蠟?zāi)#搼?yīng)用有兩種3D打印方案,一種是熔融沉積成形技術(shù),根據(jù)三維零件圖逐層打印出高分子材質(zhì)零件,最后經(jīng)過(guò)去支撐處理來(lái)改善打印件表面品質(zhì)得到打印蠟?zāi)#涣硪环N是采用光固化成形技術(shù),根據(jù)三維零件圖逐層打印出光敏樹(shù)脂、聚苯乙烯等材質(zhì)的零件,經(jīng)過(guò)去支撐處理來(lái)改善打印件表面品質(zhì)得到打印蠟?zāi)#虎坌扪a(bǔ)缺陷,采用激光立體成形技術(shù)對(duì)鈦合金鑄件中一些重要零件進(jìn)行缺陷修復(fù)成形,如在一些大面積薄壁件上進(jìn)行大體積增材修復(fù)、恢復(fù)復(fù)雜形狀結(jié)構(gòu)損傷部位的形狀和性能[13],具有變形小、提高修復(fù)件力學(xué)性能等優(yōu)勢(shì)。
1、鈦合金構(gòu)件生產(chǎn)工藝流程及特點(diǎn)
鈦的化學(xué)活性高,為避免澆注時(shí)與鑄型材料發(fā)生激烈反應(yīng),一般選擇石墨、氧化鋯、氧化釔等作為與鈦液接觸的面層鑄型材料,并逐漸發(fā)展形成機(jī)加工石墨型和熔模精密鑄造兩種傳統(tǒng)主流工藝[14],見(jiàn)圖1。在熔模鑄造中,首先要根據(jù)鈦合金零件圖,考慮澆注收縮率和加工余量等因素,進(jìn)行鑄件圖、射蠟?zāi)>邎D等工藝設(shè)計(jì),并加
工射蠟金屬模具,使用射蠟機(jī)和射蠟?zāi)>邏褐频南災(zāi)#?jīng)掛漿撒砂、干燥焙燒等工序后,完成陶瓷型殼制備,再進(jìn)行真空澆注獲得鑄件。與熔模鑄造工藝不同,機(jī)加工
石墨型是使用優(yōu)質(zhì)高純石墨加工成石墨型,再澆注獲得鈦合金鑄件。兩種工藝均存在工序流程長(zhǎng)、裝備工藝復(fù)雜、鑄型成本高的問(wèn)題。
2、3D打印技術(shù)優(yōu)勢(shì)
3D打印技術(shù)憑借無(wú)需模具、快速性、低成本、高柔性和高集成化等優(yōu)勢(shì)而被廣泛應(yīng)用[15]。根據(jù)鈦合金鑄件傳統(tǒng)生產(chǎn)工藝流程及優(yōu)缺點(diǎn),以縮短交期、降低成本、
成形復(fù)雜結(jié)構(gòu)零件為目的,3D打印金屬及模樣技術(shù)在鈦合金鑄件生產(chǎn)過(guò)程中具有顯著技術(shù)優(yōu)勢(shì),具體如下[16,17]。
(1)快速成形,縮短交期 可直接快速成形鑄件、模樣,省去模具設(shè)計(jì)、加工及試模等工序,使鈦合金鑄件交付周期由傳統(tǒng)的2~3個(gè)月,縮短至15~30天,尤其適用于鈦合金鑄件新產(chǎn)品開(kāi)發(fā)。
(2)簡(jiǎn)化流程,降低成本 一方面,3D打印無(wú)需模具、石墨型、工裝設(shè)計(jì)及加工,節(jié)省了高昂的制作費(fèi)用,特別適合于多品種、單件或小批量生產(chǎn)的鈦合金鑄件;
另一方面,利用3D 打印工藝設(shè)計(jì)及制造靈活性的特點(diǎn),實(shí)現(xiàn)零件的一體成形制造,減少傳統(tǒng)工藝多零件分體設(shè)計(jì)、制造、焊接、熱處理、機(jī)加工等復(fù)雜工序及成本,
提高材料利用率,實(shí)現(xiàn)降本增效。
(3)設(shè)計(jì)自由,生產(chǎn)柔性 3D打印技術(shù)是采用逐層堆積成形方法打印金屬、模樣,無(wú)需開(kāi)模具,不受鑄造分型、斜度等工藝設(shè)計(jì)限制,可對(duì)鑄件結(jié)構(gòu)進(jìn)行拓?fù)鋬?yōu)化
及一體化成形設(shè)計(jì),能夠制造出傳統(tǒng)工藝無(wú)法生產(chǎn)的復(fù)雜結(jié)構(gòu)鈦合金鑄件。此外,3D打印呈現(xiàn)高度數(shù)字化、信息化、集成化特點(diǎn),生產(chǎn)效率和成本受鑄件結(jié)構(gòu)影響較
小,可實(shí)現(xiàn)柔性生產(chǎn),且與傳統(tǒng)鑄造工藝相比,鈦合金鑄件品種越多、結(jié)構(gòu)越復(fù)雜、數(shù)量越有限,柔性生產(chǎn)經(jīng)濟(jì)性越顯著。
此外,3D打印鈦合金構(gòu)件作為一種先進(jìn)的一體化加工方案,可一次性完成傳統(tǒng)構(gòu)件鑄、鍛、焊、機(jī)加工等多工序制造方案,在生產(chǎn)周期、減重、綜合降本等方面優(yōu)
勢(shì)突出,應(yīng)用趨于廣泛。
3、3D打印鈦合金構(gòu)件技術(shù)及應(yīng)用
與采用傳統(tǒng)鑄造方法生產(chǎn)鈦合金構(gòu)件相比,使用金屬粉體或絲材等原料,直接3D打印制備鈦合金構(gòu)件,無(wú)需模具設(shè)計(jì)、加工、制殼、澆注、清殼等工序,從三維模型到完成構(gòu)件原型制作通常只需幾個(gè)小時(shí)到幾十個(gè)小時(shí),是目前鈦合金構(gòu)件成形流程最短、時(shí)間最快、可成形結(jié)構(gòu)最復(fù)雜的制備方法。同時(shí),3D打印鈦合金構(gòu)件為結(jié)構(gòu)設(shè)計(jì)、優(yōu)化提供了最大自由度,為分體式零件輕量化、一次性整體設(shè)計(jì)和制造提供了有效解決方案,可成形復(fù)雜、個(gè)性化結(jié)構(gòu),制作的零件無(wú)需拼焊,一致性好,解決了傳統(tǒng)方式帶來(lái)的增重、密封性差和結(jié)構(gòu)件整體強(qiáng)度剛度低等問(wèn)題。
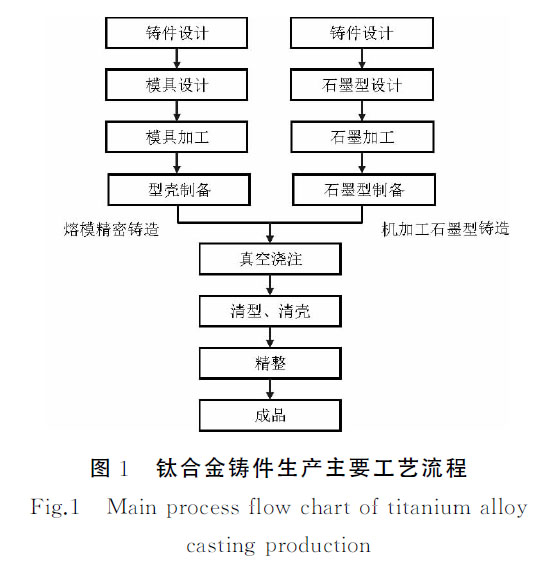
3D打印鈦合金構(gòu)件具有的上述優(yōu)勢(shì),使其在航空航天領(lǐng)域獲得了快速發(fā)展,同時(shí)在醫(yī)療、汽車(chē)、快速制造等領(lǐng)域也具有廣闊的應(yīng)用前景。在工程化應(yīng)用方面,發(fā)達(dá)國(guó)家對(duì)3D 打印鈦合金構(gòu)件技術(shù)展開(kāi)了大量研究。AeroMet公司采用3D打印技術(shù)為波音公司制造了F/A-18E/F艦載聯(lián)合殲擊機(jī)/攻擊機(jī)鈦合金次承力結(jié)構(gòu)
件,主要包括航空翼根吊環(huán)和大型鈦合金翼梁,鑄件尺寸分別達(dá)到900mm×300mm×150mm、2400mm×225mm×100mm,并實(shí)現(xiàn)了裝機(jī)應(yīng)用,見(jiàn)圖2[11]。美國(guó)空客公司在其A380客機(jī)上安裝了首個(gè)由3D打印制造的一體化設(shè)計(jì)、復(fù)雜結(jié)構(gòu)鈦合金主飛行控制液壓元件,并順利完成飛行測(cè)試,見(jiàn)圖3[11]。近年來(lái),國(guó)內(nèi)3D打印鈦合金構(gòu)件應(yīng)用發(fā)展迅速,先后研制并掌握了TA15、TC4、TC11等鈦合金大型、復(fù)雜、整體、主承力飛機(jī)關(guān)鍵構(gòu)件3D打印技術(shù),并實(shí)現(xiàn)了C919大型客機(jī)在內(nèi)的多型號(hào)飛機(jī)裝機(jī)應(yīng)用,圖4為某型號(hào)飛機(jī)“眼鏡式”鈦合金加強(qiáng)框。2012年,研制的大飛機(jī)C919中央翼緣條鈦合金3D 打印金屬通過(guò)了性能測(cè)試,其尺寸為3000mm×350mm×450mm,質(zhì)量為196kg;同時(shí),采用3D打印技術(shù)還研制了軸承座后機(jī)匣、超音速飛行器方向舵、復(fù)雜內(nèi)部結(jié)構(gòu)零件等構(gòu)件[5]。鈦合金3D打印技術(shù)在零件快速修復(fù)及制造方面優(yōu)勢(shì)顯著,可有效延長(zhǎng)零件使用壽命、減少備品備件,提升軍事裝備作戰(zhàn)能力。
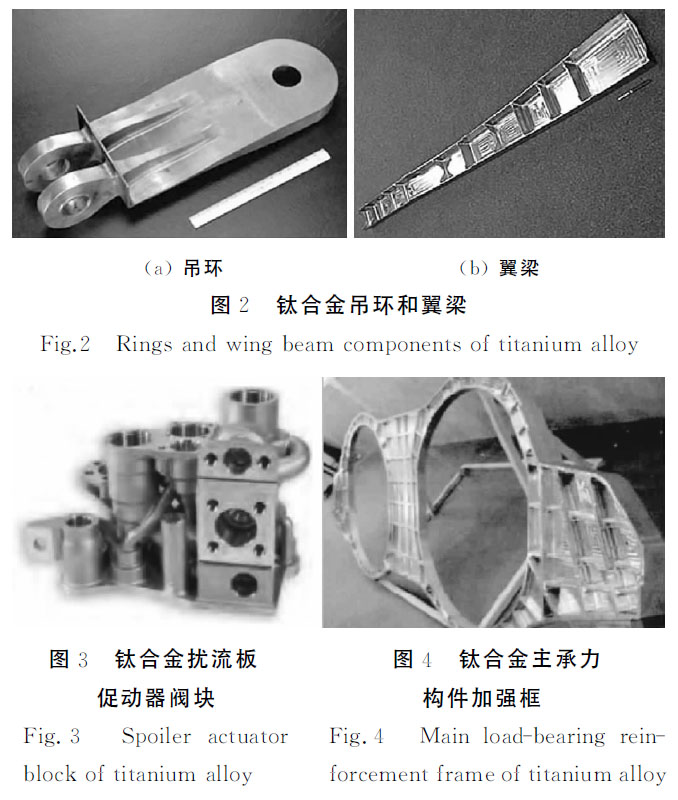
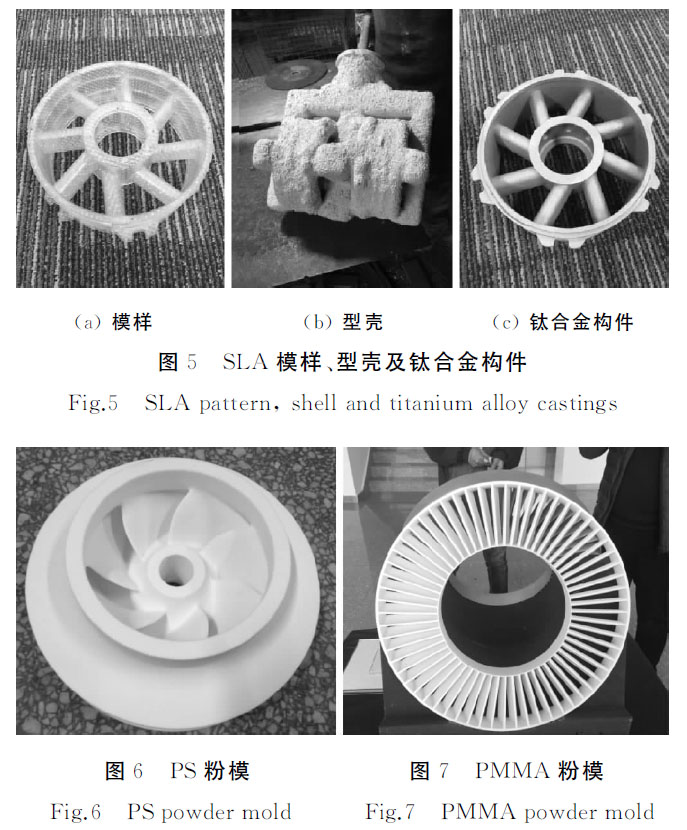
此外,3D打印技術(shù)在個(gè)性化、復(fù)雜三維結(jié)構(gòu)及難加工醫(yī)療器械制造中具有優(yōu)勢(shì),非常適合鈦合金骨科植入物醫(yī)療器械制造,使植入物外形和力學(xué)性能與人體自身骨骼
實(shí)現(xiàn)理想雙重適配,目前已經(jīng)實(shí)現(xiàn)商業(yè)化應(yīng)用[8,18]。
4、3D打印模樣技術(shù)及應(yīng)用
通過(guò)3D打印高分子材料模樣,并使用熔模鑄造鈦合金鑄件,已經(jīng)實(shí)現(xiàn)了工業(yè)化應(yīng)用。與3D打印鈦合金構(gòu)件相比,雖然生產(chǎn)流程有所增加,但由于模樣制備成本低,可獲得傳統(tǒng)鈦合金精鑄件組織性能,在鈦粉成本未實(shí)現(xiàn)大幅降低條件下,該方法用于單件、小批量,或不易開(kāi)金屬模具鈦合金鑄件生產(chǎn),能夠快速、精確地制造出任意復(fù)雜的零部件模型,在縮短生產(chǎn)周期、降低成本方面具有綜合優(yōu)勢(shì)。3D打印模樣需具備足夠強(qiáng)度和較少灰分含量,以滿足制殼抑制變形、減少澆注掉渣夾雜等品質(zhì)風(fēng)險(xiǎn)。目前,3D打印模樣材質(zhì)主要有光敏樹(shù)脂模(SLA模)、聚苯乙烯模(PS粉模)和聚甲基丙烯酸甲酯(PMMA粉模)等3種。SLA 模是基于光固化快速成形技術(shù)(SLA),以液態(tài)樹(shù)脂為原料制作而成,其生產(chǎn)的鈦合金鑄件具有尺寸精度高、表面粗糙度低等優(yōu)點(diǎn),但制模成本高于另外兩種工藝。圖5為SLA模樣、型殼及鈦合金鑄件。PS粉模(見(jiàn)圖6)和PMMA粉模(見(jiàn)圖7)相似,分別采用顆粒燒結(jié)和粘結(jié)方法制模,雖然成本較低,但尺寸精度和表面粗糙度不及SLA 模。3種打印模樣技術(shù)特點(diǎn)、成本對(duì)比情況見(jiàn)表1,需要在實(shí)際生產(chǎn)中,根據(jù)品質(zhì)要求和成本因素綜合考慮[19,20]。
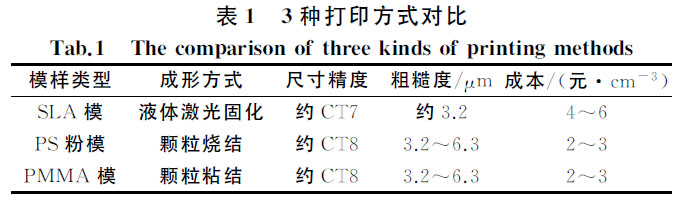
5、存在的問(wèn)題及發(fā)展趨勢(shì)
與鋼鐵、鋁合金鑄件不同,鈦合金鑄件昂貴、產(chǎn)量低、結(jié)構(gòu)復(fù)雜,因此非常適宜采用3D打印技術(shù),以降低鑄件綜合成本,縮短生產(chǎn)周期。近年來(lái),3D打印技術(shù)在鈦合金鑄件生產(chǎn)中雖然實(shí)現(xiàn)了快速應(yīng)用,但仍然存在產(chǎn)業(yè)發(fā)展瓶頸,需要整個(gè)產(chǎn)業(yè)鏈企業(yè)共同努力解決[16,21]。存在的問(wèn)題及發(fā)展趨勢(shì)主要包括4個(gè)方面。
(1)提高3D 打印鈦合金構(gòu)件品質(zhì)及穩(wěn)定性 粉體、絲棒材等鈦合金打印原料加工性能不佳,以及打印設(shè)備、參數(shù)不當(dāng),均會(huì)導(dǎo)致鈦合金零件出現(xiàn)球化、裂紋、空隙及翹曲變形等問(wèn)題,實(shí)現(xiàn)細(xì)粒徑、低氧含量、高球形度合金粉末的制備,并持續(xù)從打印原料、打印設(shè)備和工藝等方面進(jìn)行系統(tǒng)整體發(fā)展和提升,以保證鑄件的品質(zhì)和穩(wěn)定性。
(2)降低生產(chǎn)成本 盡管3D打印技術(shù)能夠簡(jiǎn)化鈦合金鑄件生產(chǎn)工藝流程,提高原料利用率,但由于鈦合金粉體價(jià)格昂貴,使得3D打印鈦合金構(gòu)件成本居高不下。因此,創(chuàng)新制粉工藝技術(shù),大幅降低鈦合金粉體成本,同時(shí)推進(jìn)SLA模、PS粉模、PMMA粉模降低成本,是實(shí)現(xiàn)3D打印技術(shù)在鈦合金鑄件生產(chǎn)中廣泛應(yīng)用的基礎(chǔ)。
(3)提高技術(shù)成熟度,建立完善的標(biāo)準(zhǔn)體系 搜集整理數(shù)據(jù),加大3D打印鈦合金構(gòu)件應(yīng)用評(píng)價(jià);同時(shí),需要行業(yè)整合資源,發(fā)展并建立鈦合金粉體、3D打印裝備
和工藝、3D打印鈦合金構(gòu)件及其無(wú)損檢測(cè)方法和標(biāo)準(zhǔn)體系,為應(yīng)用領(lǐng)域設(shè)計(jì)人員提供可靠標(biāo)準(zhǔn)體系支撐,是影響3D打印技術(shù)進(jìn)一步發(fā)展的決定因素。
(4)3D打印型殼新技術(shù)發(fā)展 陶瓷3D打印是近年來(lái)剛興起的一種快速成形技術(shù),將其應(yīng)用于傳統(tǒng)鈦合金熔模精密鑄造工藝中,使陶瓷膏體直接打印型殼來(lái)取代傳統(tǒng)的模樣制備,與3D打印模樣相比,不僅可以進(jìn)一步縮短流程,同時(shí)可避免模樣灰分殘留、脹殼導(dǎo)致的鈦合金鑄件掉渣夾雜等品質(zhì)問(wèn)題。
6、結(jié)語(yǔ)
綜述了3D打印技術(shù)在鈦合金構(gòu)件和模樣領(lǐng)域的研究現(xiàn)狀和發(fā)展問(wèn)題,3D打印金屬及模樣作為一項(xiàng)前沿技術(shù),均已在鈦合金鑄件生產(chǎn)中獲得應(yīng)用,為單件小批量鑄件快速、低成本制造,實(shí)現(xiàn)特殊復(fù)雜結(jié)構(gòu)零件成形提供了解決方案。但新技術(shù)仍然存在不足,需要持續(xù)進(jìn)行技術(shù)創(chuàng)新和改善提升,以實(shí)現(xiàn)進(jìn)一步廣泛應(yīng)用。
參考文獻(xiàn)
[1]王新英,謝成木.國(guó)內(nèi)外鈦合金精密鑄造型殼材料的發(fā)展概況[J].特種鑄造及有色合金,2001(3):40-42.
[2]YEONG W Y,CHUA C K,LEONG K F,et al.Rapid proto typing in tissueengineering:Challenges and potential[J].Trends in Biotechnology,2004,22(12):643-652.
[3]SALLICA L E,JARDINI A L,F(xiàn)OGAGNOLO J B.Microstructureand mechanical behavior of porous Ti-6Al-4Vparts obtained by selective
laser melting[J].Journal of the Mechanical Behavior of Biomedical
Materials,2013,26:98-108.
[4]WOHLERS T,CAFFREY T.Additive manufacturing:The stateofthe industry[J].Manufacturing Engineering,2016,156(5):45-52.
[5]范李鵬,王寶兵,余國(guó)康.鈦合金復(fù)雜薄壁結(jié)構(gòu)件精密鑄造工藝研究[J].特種鑄造及有色合金,2016,36(10):1 079-1 081.
[6]高婷,趙亮,馬保飛,等.鈦合金鑄造技術(shù)現(xiàn)狀及發(fā)展趨勢(shì)[J].熱加工工藝,2014,43(21):5-11.
[7]王紅紅,劉振軍,王紅.鈦合金鑄件的應(yīng)用及發(fā)展[J].新材料產(chǎn)業(yè),2009(11):25-30.
[8]DUTTA B,F(xiàn)ROES F H.Additive manufacturing of titanium alloys[J].Advanced Materials and Processes,2014,172(2):18-23.
[9]劉時(shí)兵,柴皓,倪嘉,等.航空航天用鈦合金3D打印技術(shù)的研究概述[J].鑄造,2019,68(9):965-970.
[10]CARRICO J D,LEANG K K.Fused filament 3Dprinting of ionicpolymer-metal composites for soft robotics[A].ElectroactivePolymer Actuators and Devices[C].Portland,2017.
[11]WALKER J,HARRIS E,LYNAGH C,et al.3Dprinted smartmolds for sand casting[J].International Journal of Metalcasting,
2018(3):1-12.
[12]沈選金,賀同正,羅國(guó)軍,等.鈦及其合金的熔模精密鑄造[J].鑄造技術(shù),2015,36(7):1 876-1 878.
[13]杜宇雷,孫菲菲,原光,等.3D打印材料的發(fā)展現(xiàn)狀[J].徐州工程學(xué)院學(xué)報(bào)(自然科學(xué)版),2014,29(1):20-24.
[14]KANG J,MA Q.The role and impact of 3Dprinting technologiesin casting[J].China Foundry,2017,14(3):157-168.
[15]ALMAGHARIZ E S,CONNER B P,LENNER L,et al.Quantifying the role of part designcomplexity in using 3Dsand printingfor molds and cores[J].International Journal of Metalcasting,2016,10(3):240-252.
[16]張馳,趙航,孫曉紅,等.航天耐高溫鈦合金零件3D打印質(zhì)量?jī)?yōu)化研究[J].計(jì)算機(jī)仿真,2017,34(3):88-91.
[17]唐超蘭,溫竟青,張偉祥,等.鈦合金3D打印成形技術(shù)及缺陷[J].航空材料學(xué)報(bào),2019,39(1):38-47.
[18]馬晨璐.鈦合金及3D打印在汽車(chē)行業(yè)的應(yīng)用[J].中國(guó)鈦業(yè),2018(1):16-19.
[19]BROWN A.3Dprinting in insructional settings:Identifying acurricular hierarchy of activities[J].Tech.Trends,2015,59(5):16-24.
[20]吳復(fù)堯,劉黎明,許沂,等.3D打印技術(shù)在國(guó)外航空航天領(lǐng)域的發(fā)展動(dòng)態(tài)[J].飛航導(dǎo)彈,2013(12):10-15.
[21]喬海濱,袁兵兵,孫宏喆,等.3D打印熔模精密鑄造模樣燃燒特性對(duì)比研究[J].鑄造技術(shù),2020,41(6):544-547.
相關(guān)鏈接