1、引言
提高鈦合金螺絲的加工效率、減少零件加工變形一直是鈦合金加工過(guò)程中的研究重點(diǎn)。鈦合金高速加工可有效降低零件的變形量,是鈦合金螺絲加工的研究方向 。本文在分析鈦合金異形零件加 工方案的基礎(chǔ)上,針對(duì)實(shí)際加工過(guò)程中影響加工效率的問(wèn)題提出新的工藝方案:采用高速銑削對(duì)零件進(jìn)行粗加工,并根據(jù)零件結(jié)構(gòu)特點(diǎn)將零件劃分為不同加工區(qū)域,分析確定各加工區(qū)域的加工順序,對(duì)零件進(jìn)行精加工。通過(guò)對(duì)工藝的優(yōu)化,使零件加工變形得到了有效控制,而且加工效率得到明顯提高。
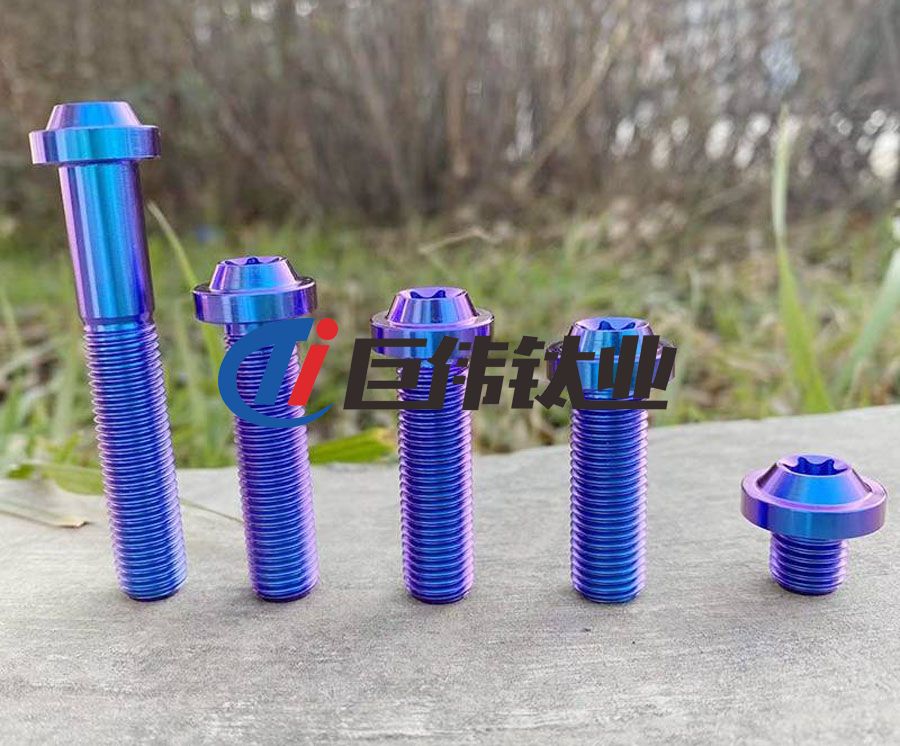
2、零件加工方案分析
2.1 零件加工方案
如圖 1 所示,某機(jī)型鈦合金螺絲呈“人” 字形, 零件外廓尺寸約1000mm×600mm×70mm,零件頭部厚度為27mm,腹板厚度從緊鄰頭部腹板到腿部腹板逐漸減小,緊鄰頭部腹板厚度為6mm,腿部腹板厚度為2mm。
鈦合金異形零件原加工方案為:粗銑外形→粗銑第一面內(nèi)形→粗銑第二面內(nèi)形→精銑第二面內(nèi)形→精銑第一面內(nèi)形→精銑外形→銑切零件工藝凸臺(tái),所用刀具為立銑刀。零件加工仿真結(jié)果見圖2。
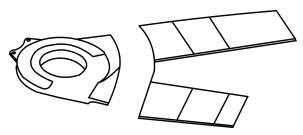
圖 1 某機(jī)型鈦合金螺絲
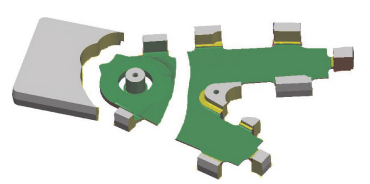
圖 2 零件加工仿真結(jié)果
2.2 加工方案分析
通過(guò)對(duì)原加工方案進(jìn)行分析,提出如下問(wèn)題:①鈦合金螺絲毛料為模鍛件,材料較大,銑外形工作量大,采用上述方案加工零件,毛料最終去除量約占毛坯料重量的70% ;銑外形工序的毛料去除量約占毛壞料總?cè)コ康?0% 。由于銑外形工序?yàn)榉窃鲋倒ば颍ú恢苯赢a(chǎn)生生產(chǎn)價(jià)值的工序),因此,若將該工序優(yōu)化或取消,將大幅提高零件加工效率;②采用上述方案加工零件,在實(shí)際加工過(guò)程中,腿部腹板處易發(fā)生翹曲變形,導(dǎo)致零件型面檢測(cè)出現(xiàn)問(wèn)題;③ 銑外形工序?qū)喊鍞[放位置要求嚴(yán)格,若壓板位置出現(xiàn)偏差,容易出現(xiàn)刀具與壓板相撞的加工事故。因此,銑外形時(shí),需要操作人員時(shí)刻留意刀具與壓板是否會(huì)發(fā)生碰撞,浪費(fèi)大量精力;④分析可知,銑外形工序需要在開敞式機(jī)床上進(jìn)行加工,以便于觀察零件加 工狀態(tài),但目前主流機(jī)床為封閉或半封閉式機(jī)床,無(wú) 法直觀查看零件的加工狀態(tài),容易出現(xiàn)加工事故。
綜上所述,該零件加工方案急需進(jìn)行工藝優(yōu)化改進(jìn),可優(yōu)化點(diǎn)分析如下:
①由于銑外形工序?yàn)榉窃鲋倒ば颍庸すぷ髁空伎偧庸すぷ髁勘戎剌^大,且銑外形過(guò)程中極易出現(xiàn)加工事故,可取消銑外形工序;②立銑刀粗加工零件時(shí),切削深度大,切削速度慢,易造成零件變形,可 采用高速銑削進(jìn)行零件粗加工,留少量余量,再利用立銑刀進(jìn)行零件精加工;③零件精加工時(shí),腹板厚度不同,剛度不同。若不分區(qū)域加工,薄處腹板容易因相鄰腹板不能提供足夠剛度而發(fā)生振顫,需根據(jù)腹板厚度,結(jié)合零件自身結(jié)構(gòu)特點(diǎn)進(jìn)行加工區(qū)域劃分, 并合理規(guī)劃各區(qū)域加工順序進(jìn)行零件精加工。
3、零件加工工藝優(yōu)化
通過(guò)對(duì)零件加工方案進(jìn)行分析,結(jié)合可優(yōu)化點(diǎn)分析,從工藝流程優(yōu)化、粗加工優(yōu)化及精加工優(yōu)化三個(gè)部分對(duì)該鈦合金異形零件進(jìn)行加工工藝優(yōu)化。
3.1 加工工藝流程優(yōu)化
異形鈦合金螺絲在銑切外形時(shí)存在諸多弊端, 因此,在工藝流程優(yōu)化過(guò)程中,取消銑切外形工序, 直接進(jìn)行零件內(nèi)形的加工,并在加工過(guò)程中引入鈦合金高速銑削加工技術(shù)。優(yōu)化后的加工工藝流程見圖 3。具體加工過(guò)程:①采用高速銑削加工技術(shù)進(jìn)行零件粗加工,以減小因毛料去除量大所引起的加工變形;②根據(jù)零件 結(jié)構(gòu)特點(diǎn)對(duì)零件加工區(qū)域進(jìn)行劃分及排序,完成零件精加工。
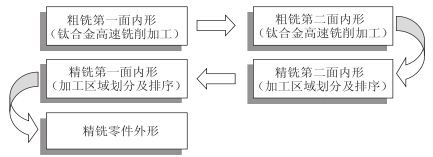
圖 3 加工工藝流程優(yōu)化
3.2 鈦合金高速銑削加工技術(shù)
切削線速度達(dá)到100m/min以上的鈦合金切削方式被稱為高速切削 。高速銑削是鈦合金螺絲銑削加工的發(fā)展方向,具有加工效率高、切削熱量少及切削振動(dòng)小的特點(diǎn) ,不僅能夠提高零件加工效率,還可有效減小零件變形量。
由于零件腿部腹板較薄,粗加工材料去除量大, 在實(shí)際加工中極易發(fā)生翹曲變形,因此將高速銑削引入零件粗加工過(guò)程,充分利用高速銑削中切削力小、引起零件變形量小的特點(diǎn)進(jìn)行該鈦合金異形零件的粗加工。該鈦合金異形零件高速銑削粗加工時(shí),使用φ63R4淺切刀,考慮到零件最終的表面粗糙度及光度要求,零件粗加工后留0.5mm余量,利用立銑刀進(jìn)行精加工,加工參數(shù)設(shè)置見表1。
表1 鈦合金異形零件高速銑削加工參數(shù)

3.3 零件加工區(qū)域劃分及加工順序規(guī)劃
該鈦合金異形零件的腹板厚度從緊鄰頭部腹板到腿部腹板逐漸減薄,緊鄰頭部腹板厚度為6mm, 腿部腹板厚度為2mm。在精加工過(guò)程中,為保證腹板在加工時(shí)的剛度要求,避免發(fā)生振顫造成厚度超差,根據(jù)零件自身結(jié)構(gòu)特點(diǎn),將腹板劃分為12個(gè)區(qū)域(見圖 4)。加工順序由小到大排列,加工腹板厚度由薄到厚,使得在加工薄處腹板時(shí),相鄰腹板面可為其提供足夠剛度,從而避免發(fā)生震顫。該零件頭部厚度為27mm,不存在切削震顫問(wèn)題,放至最后加工,采用φ25R4硬質(zhì)合金刀具進(jìn)行精加工。

圖 4 零件加工區(qū)域劃分
該鈦合金異形零件正反面結(jié)構(gòu)類似,均采用相同的區(qū)域劃分方法進(jìn)行加工。采用優(yōu)化后的工藝方案加工零件,不僅將零件加工效率提升40% ,還避免了零件腿部腹板發(fā)生翹曲變形,該優(yōu)化方案已成功應(yīng)用到實(shí)際加工中。利用優(yōu)化后的方案加工零件,仿真結(jié)果見圖5。
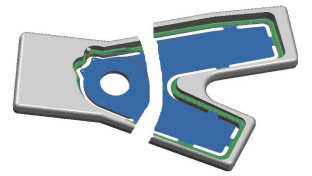
圖5 優(yōu)化后加工方案的仿真結(jié)果
4、結(jié)語(yǔ)
提高鈦合金螺絲加工效率和減小零件加工過(guò)程中的變形是鈦合金螺絲加工過(guò)程中的重要研究課題。針對(duì)某機(jī)型鈦合金異形零件加工方案所存在的問(wèn)題,提出加工工藝優(yōu)化方法:將高速銑削技術(shù)應(yīng)用到鈦合金異形零件粗加工過(guò)程中,并根據(jù)零件特點(diǎn)將腹板進(jìn)行區(qū)域劃分,規(guī)劃各區(qū)域加工順序,進(jìn)行零件精加工。
采用優(yōu)化后工藝方案加工零件發(fā)現(xiàn),加工效率明顯提升。本文工藝優(yōu)化分析方法對(duì)后續(xù)類似結(jié)構(gòu)的鈦合金螺絲加工具有一定借鑒意義。
相關(guān)鏈接